2023 Energy & Environment Award Winners
The 2023 Energy and Environment Awards recognize outstanding environmental and community relations efforts that go above and beyond what is required. Submissions from plants across the
U.S. were evaluated and recognized for environmental efforts completed in 2022.
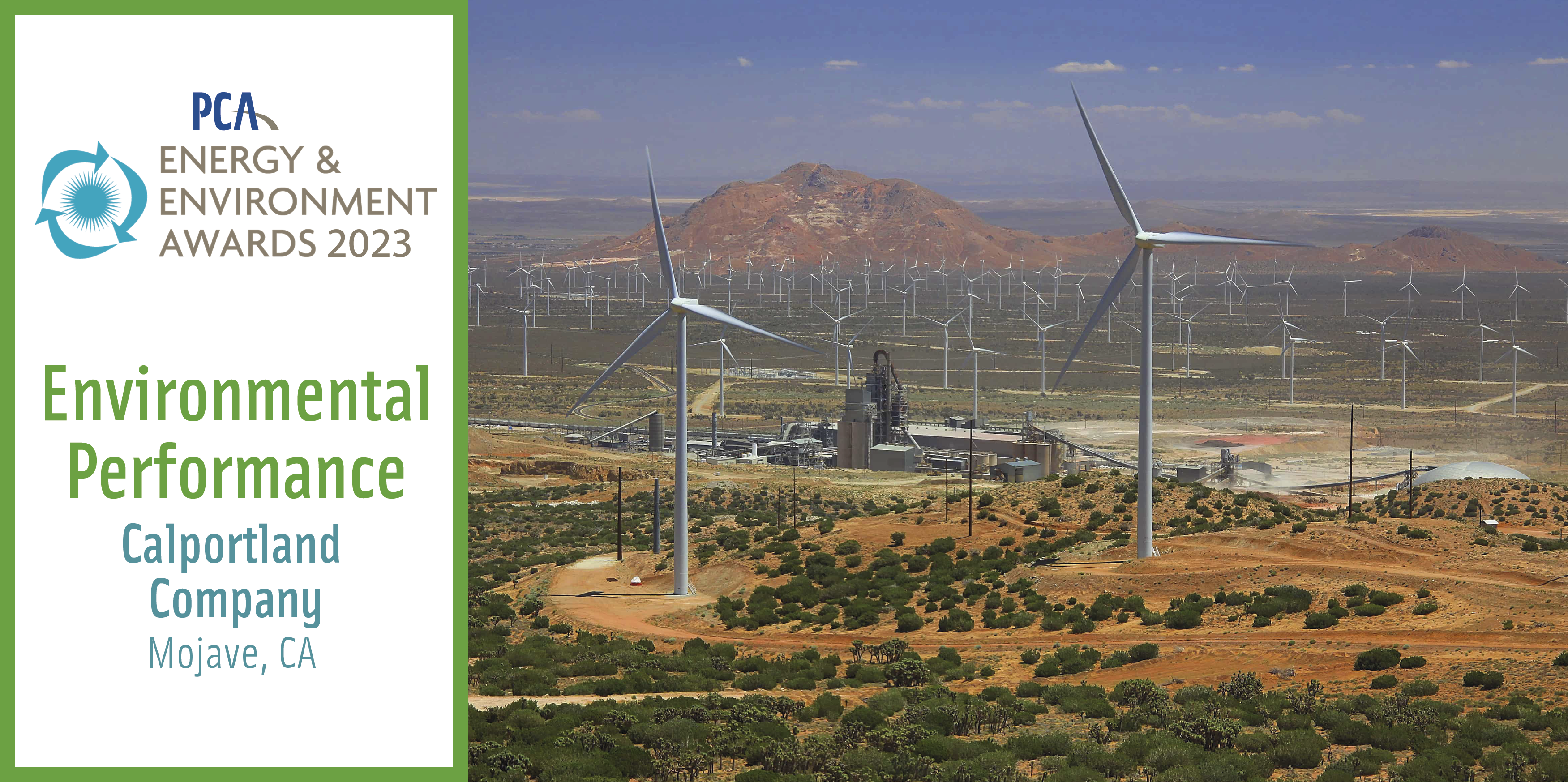
CalPortland successfully permitted a greenfield mine site that provides a cement-friendly carbon-neutral material to its Mojave Cement Plant. The carbon-neutral material is volcanic tuff which is a pozzolan material that reduces CO2 on a ton-per-ton basis when combined with clinker. The project was carefully designed by engineers, legal consultants, and over a dozen technical consultants. All of these professionals ensured the careful design of the mining area to avoid potential environmental impacts to the maximum extent possible. Numerous iterations of mining areas and designs were evaluated with the final version being the least impactful way to recover the critical resource. Implementing the use of Gem Hill pozzolan will allow CalPortland’s Mojave Cement Plant to achieve environmental goals while bolstering economic growth.
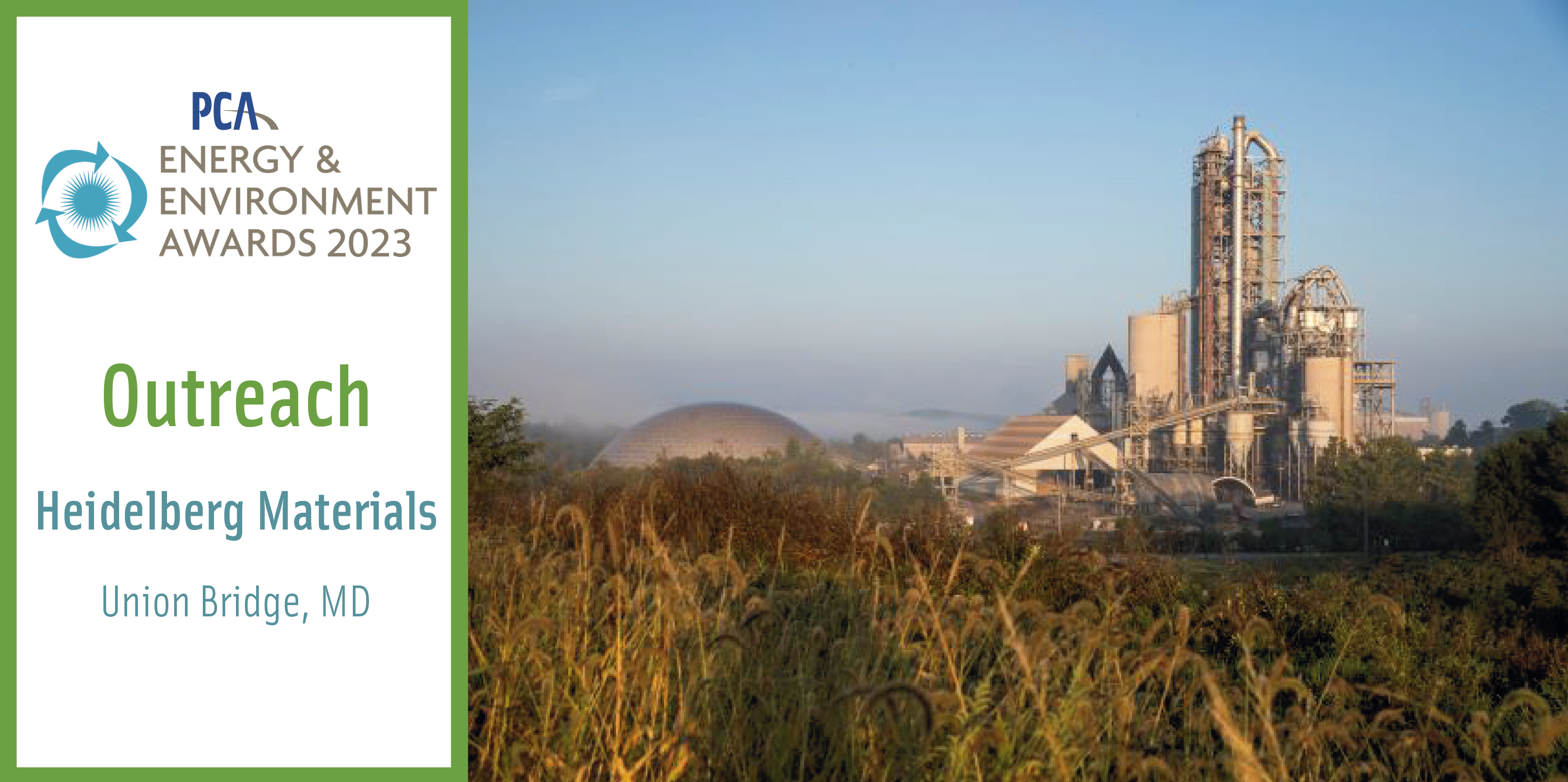
The State of Maryland made a substantial move forward in greenhouse gas emission reduction with the passage of the Climate Solutions Now Act in 2022, which calls for Maryland to reach “net zero” by 2045. Heidelberg Materials engaged with policymakers in Maryland to help shape the state’s program and provide key input into the State’s goals through a transparent and interactive engagement strategy. Heidelberg Material’s engagement included multiple interactions with stakeholders from the Maryland Energy Administration, the Maryland Department of the Environment, the Maryland Department of Labor, and the U.S. Department of Energy. During the time of policy development, Heidelberg Materials also began discussions with the University of Maryland’s Center for Global Sustainability which was tasked with gathering information about options to reduce CO2 in Maryland’s manufacturing sector. Outcomes from the engagement included education and a better understanding on the part of Maryland policymakers around the need for multiple levers to reach carbon neutrality, opportunities with near-term “wins” such as fuel conversion to lower-carbon intensity sources, and the importance of supporting infrastructure for carbon transport. In addition, Heidelberg Materials outlined strategies related to future investment, low-carbon procurement policy, as well as consideration of full life cycle approaches in evaluating the overall CO2 impacts, and how they factor into the circular economy.
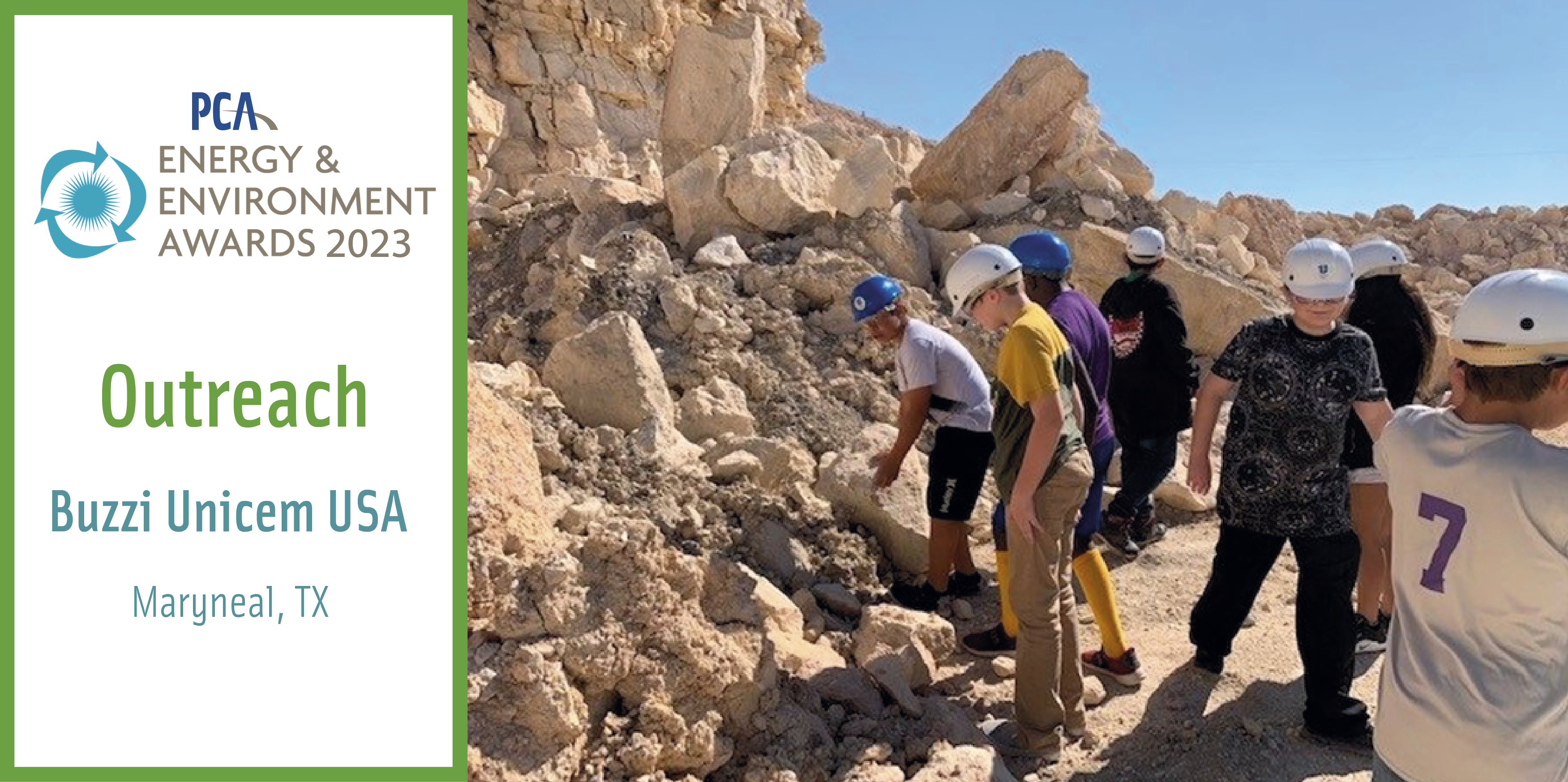
In 2022, Buzzi Unicem’s Maryneal Plant was involved in numerous educational and community outreach projects and invested more than $125,000 in donations, sponsorships, and contributions. These projects have been integral in building a solid relationship between the Plant and the community members.
During a tour of the Sweetwater High School’s Agriculture and Welding departments, the Plant Manager and a school instructor discussed the need for more specialized and updated equipment to enhance the classroom curriculum. As a result of that conversation, Buzzi Unicem management purchased a lathe and milling machine and donated them to Sweetwater High School. Additionally, teachers received training from Maryneal’s Maintenance Manager on operating the equipment.
Another initiative sponsored by the plant was the “Kids on the Land” program, where 180 local children enjoyed hands-on learning about habitats, conservation, and sustainability by exploring 69 Ranch – Buzzi’s southern neighbor. The students also enjoyed cement-making experiments along with learning about STEM careers in cement.
Finally, another outstanding community project involved the renovation of the Maryneal Community Center. The Community Center’s interior was in need of repair. Buzzi Unicem’s dedicated employees spent their scheduled work hours at the Center, bringing their expertise in electrical wiring and floor installation. Improving the Community Center has provided connection, shared pride, and a renewed gathering place for both the community of Maryneal and Buzzi Unicem employees to enjoy.
In 2022, Ash Grove’s Louisville Plant completed an important project for emissions reduction in trialing, permitting, and then starting the production of calcined clay on the ACL Kiln. This process was an innovative use of an existing kiln line to produce calcined clay while maintaining the ability to produce clinker when needed. The ACL Kiln can transition from traditional clinker to calcined clay and then back to clinker. There is very little downtime between these transitions.
Ash Grove’s facility currently uses fly ash as a Secondary Cementitious Material (SCM) in its Finish Mills to produce Duracem. Calcined clay is used as a substitute for fly ash. Using calcined clay that is produced on-site reduces the transportation emissions of SCM utilized in the Finish Mills. Ash Grove can also utilize a large amount of calcined clay in its cement while meeting all quality benchmarks. These factors resulted in a significant decrease in the overall emission per ton of cement produced at the facility.
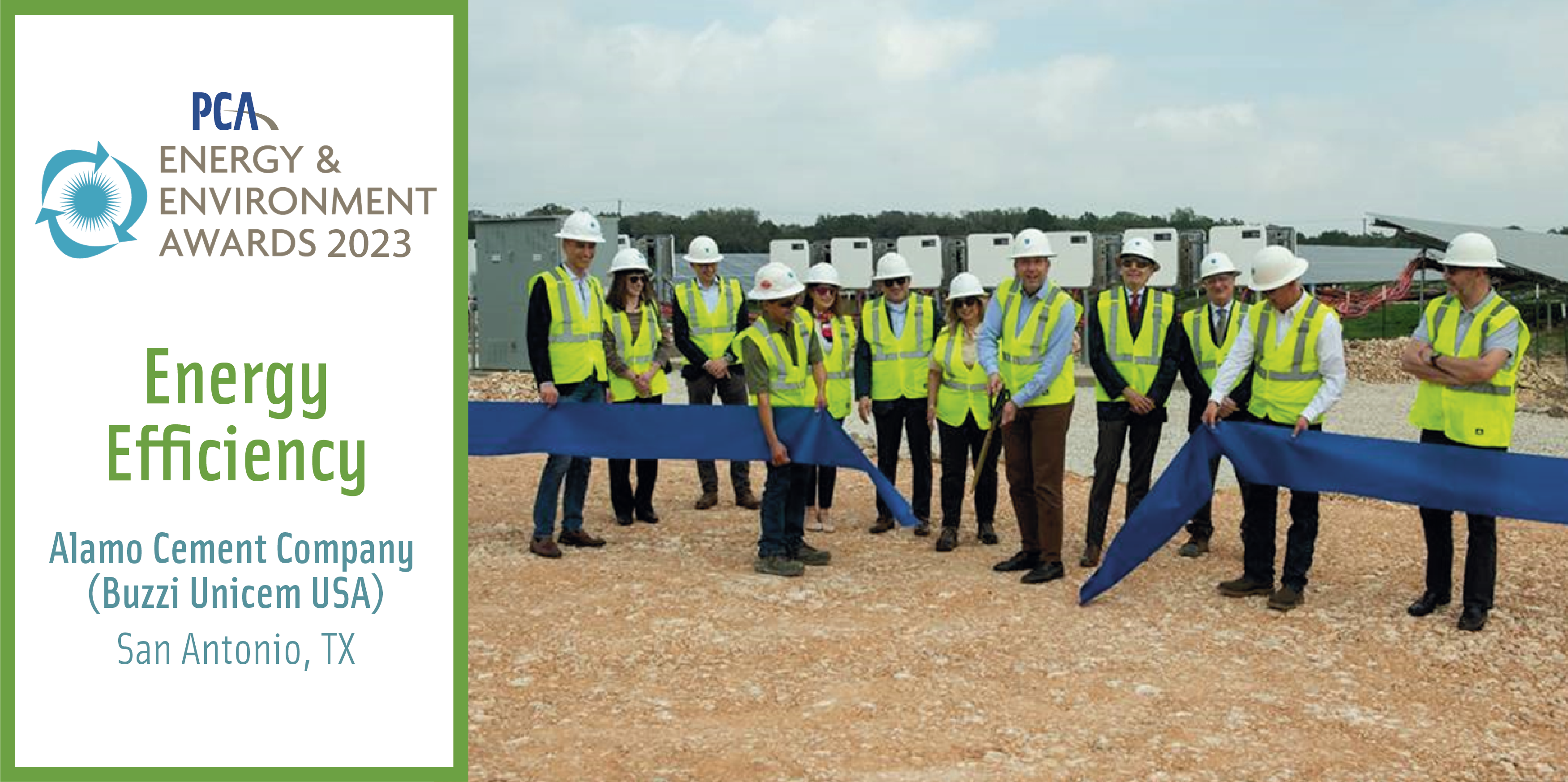
As one of Buzzi Unicem USA’s first investments to be completed on the Roadmap to Carbon Neutrality, Alamo Cement Company finished construction of their on-site solar power farm in late November 2022. The project began in early 2020 and took over two and half years from start to finish, overcoming supply chain issues brought about by the pandemic. The solar farm now covers 42 acres of plant property and contains nearly 25,000 modules and produces energy entirely for on-site plant usage. There are two separate systems that provide electricity to different parts of the production process. One supplies electricity to pyro-processing, raw material grinding, and crushing, and the other feeds finish mills, conveying, and cement shipping and packing. The installation is completely behind the meter, thereby avoiding the transmission loss that occurs with power from the grid resulting in improved energy efficiency. It is expected that the solar power generated from this project will contribute to 15% of the total cement plant power consumption at a capacity of 17,800 megawatt-hours per year.
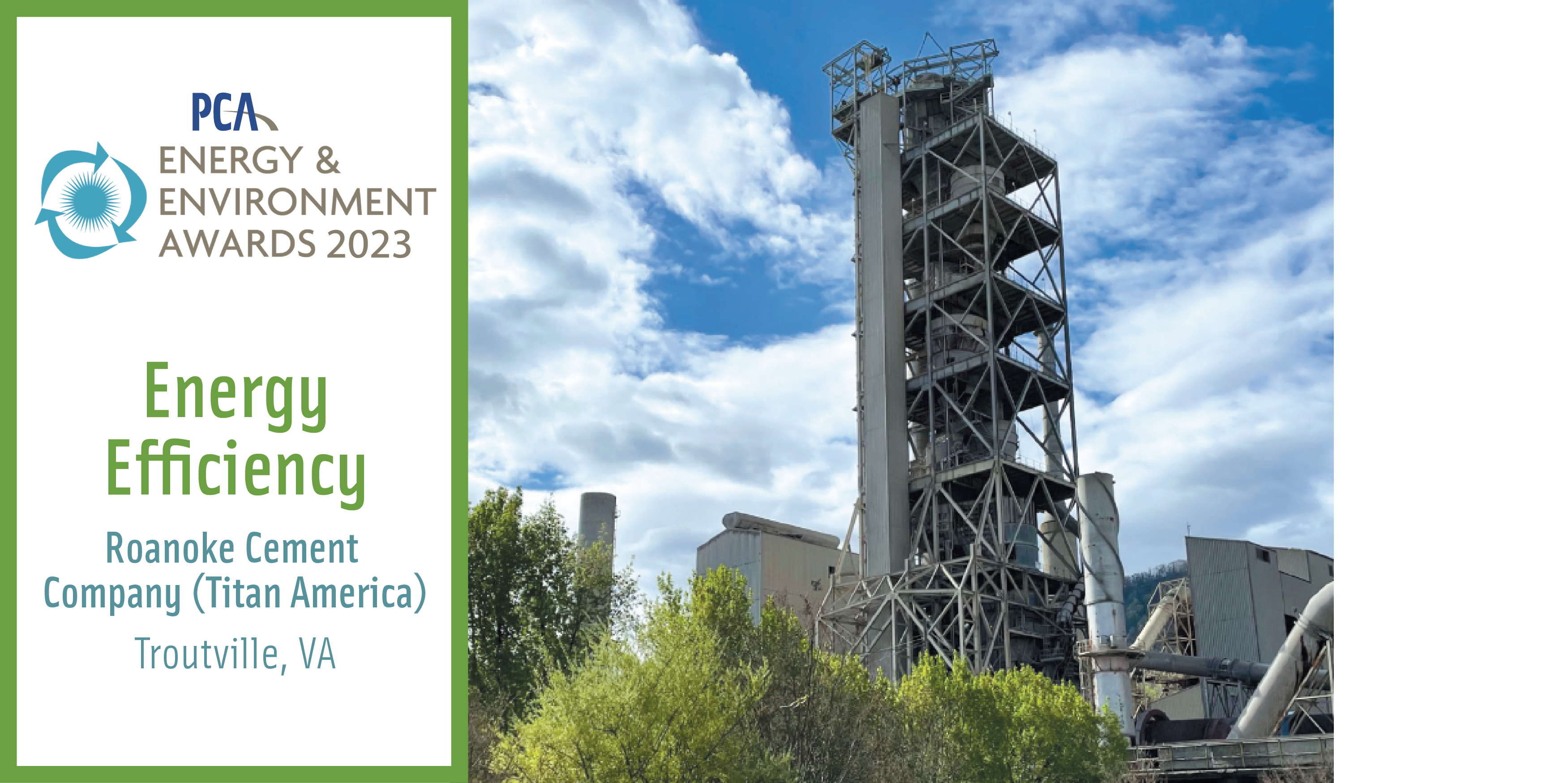
Titan America’s Roanoke Cement Company (RCC) made vast improvements in 2022 and over the last five years in areas of energy savings, air quality, water management, waste minimization, and wildlife habitat reclamation at its Troutville Plant. RCC has created long-term alliances with EPA ENERGY STAR, ISO 50001 Energy Management, Green Business Certification’s (GBCI) TRUE Zero Waste, and PCA that help develop environmental and energy-saving strategies and measure its performance and achievements. RCC’s sustainability program has achieved international recognition, particularly in Energy Management. RCC earned 16 consecutive EPA ENERGY STAR honors and is one of only two cement plants in the country to meet the ISO 50001 standard.
RCC has completely transitioned from ordinary portland cement to Type IL portland-limestone cement, which has approximately 15% lower global warming potential (CO2 – equivalent). With significant alternative fuels use and a recipient of Zero Waste certification at the gold level, RCC was recognized by the USGBC. RCC was also recognized by the Commonwealth of Virginia as the silver medal recipient of the 2022 Sustainability Program Award for its energy performance and other sustainable practices. RCC was the top industrial applicant in the category.
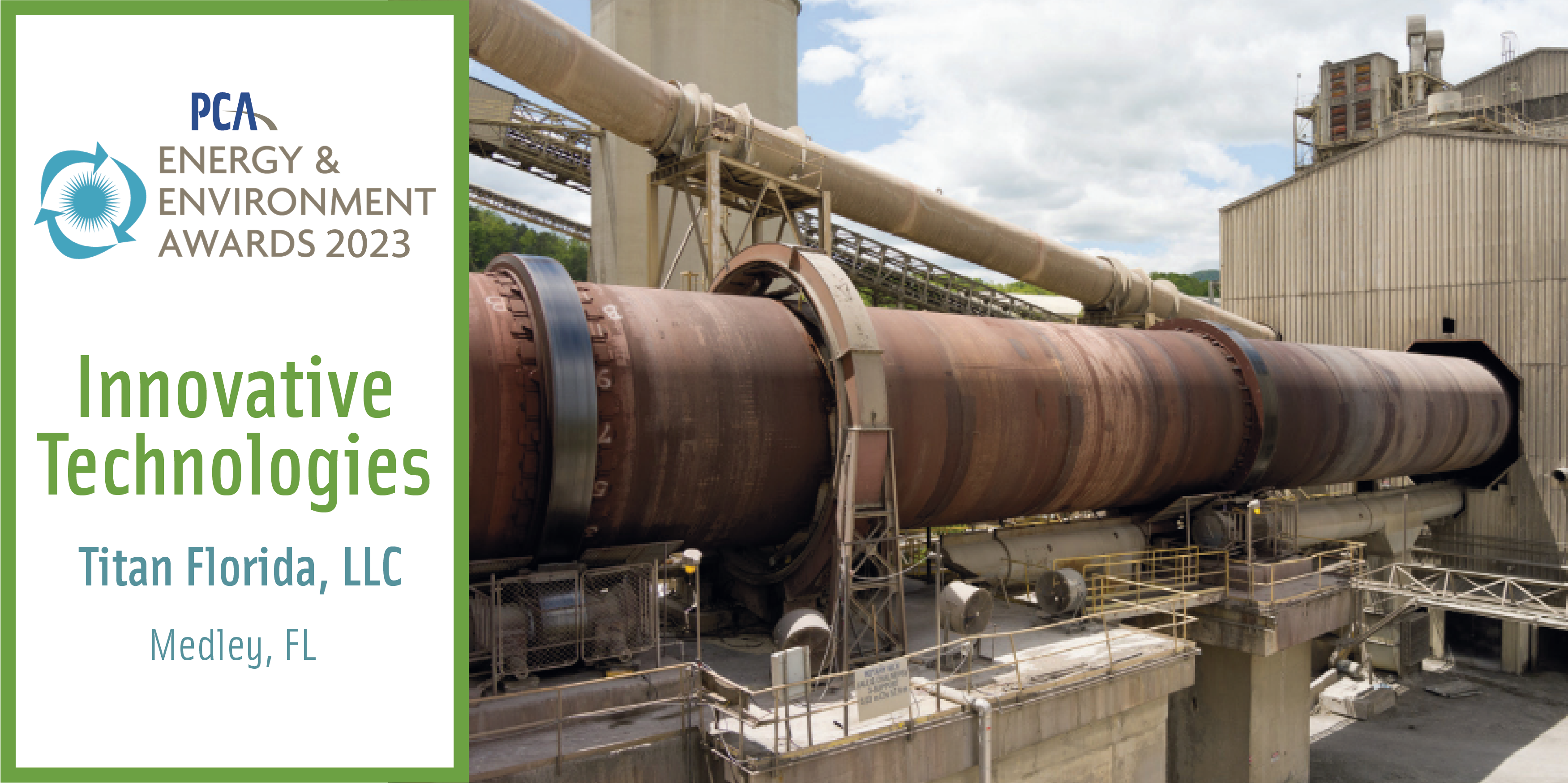
In 2022, Titan America’s Pennsuco plant (PNS), moved beyond its initial successes with artificial intelligence (AI). By utilizing sensors and signals to map a “digital twin” for normalized plant operations, and then analyzing in real-time deviations in temperature, pressure, vibration, lubrication, and other parameters, the AI models provided powerful solutions to drive production outputs and equipment effectiveness to new higher levels, while improving energy efficiency. Building on years of strong effort in digitalization, PNS improved optimization, combining the process and maintenance AI systems to achieve increased Overall Equipment Effectiveness, better process stability with higher Alternative Fuel (AF) rates, and lower energy consumption.
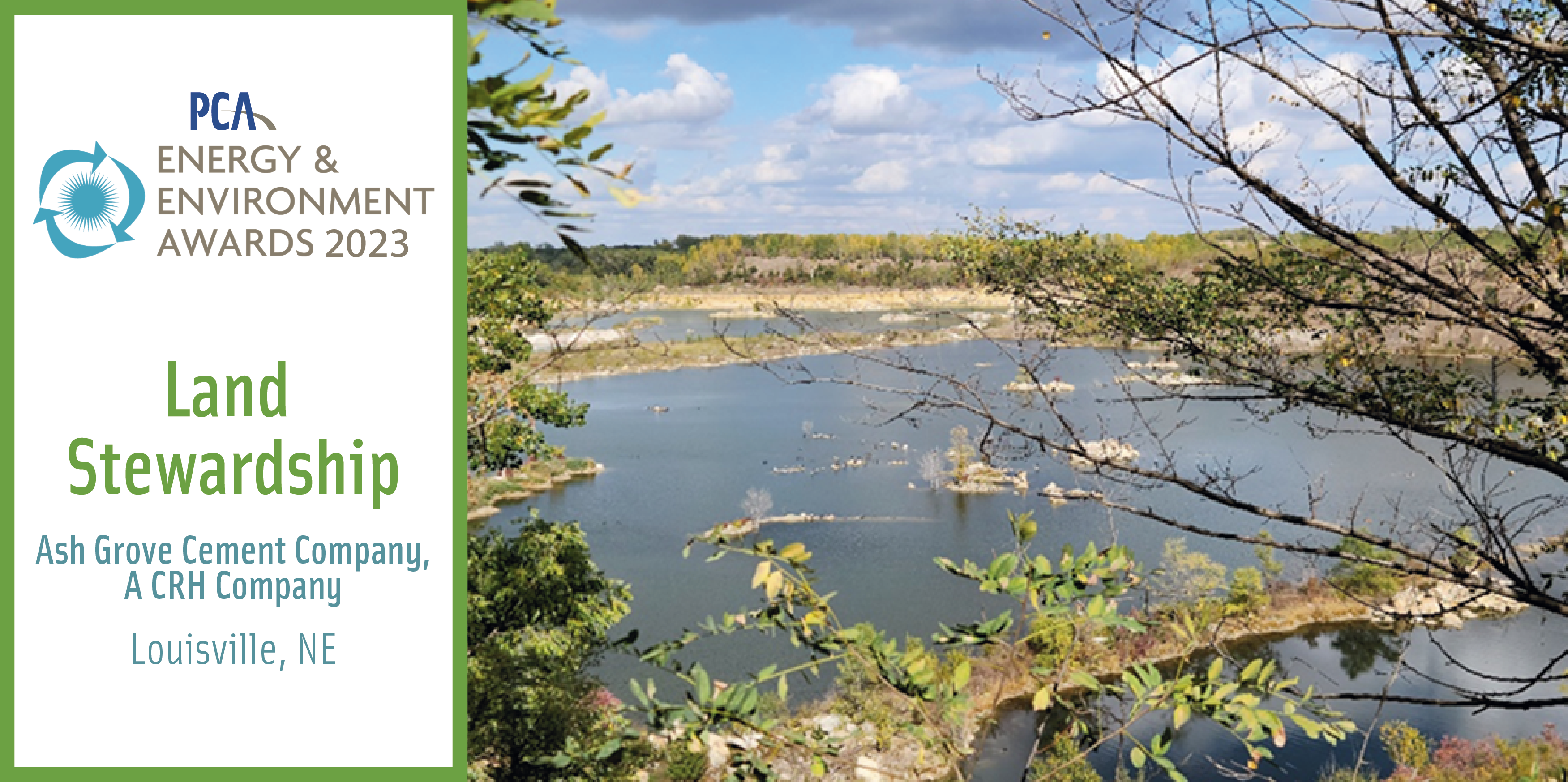
Ash Grove Louisville Plant completed work maintaining the West Quarry at its plant, to serve as a habitat area for many plants and animals. Work was done on the West end of the West Quarry to contain water in the quarry and reduce the levels of discharged Total Suspended Solids. Utilizing the quarry for settling increased the quality of water that is discharged from our site, which is a stop for migratory fowl.
East Quarry is now utilizing a continuous miner for its primary mining operations. Previously, the Louisville Plant utilized traditional drilling and blasting methods to mine the quarry, which resulted in uncontrolled dust emissions and noise disturbances. The new continuous miner allows the Louisville Plant to selectively mine an exposed ledge to obtain the correct balance of rock to feed its operation while generating less waste rock.