Occupational Health & Safety
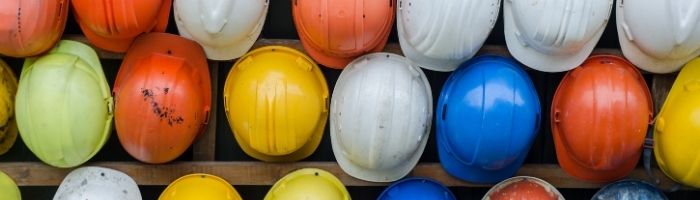
Contact Information:
Tom Harman
Senior Director, Environment, Health and Safety
tharman@cement.org
Background:
Cement is an essential component in concrete, an irreplaceable building material that is the building block of modern society. It is at the foundation of our national economy thanks to its role in providing the safe, sustainable, and resilient transportation and infrastructure on which we rely. But despite cement's critical role in our lives, there is one resource valued above all others: the men and women who work in our industry in.
The cement industry is regulated as part of the mining industry in the United States, and strict health and safety regulations must be followed at every plant and distribution site across the country. The Mine Safety and Health Administration (MSHA) is statutorily required to inspect all surface mines and facilities at least two times each year, and operations such as underground stone mines are inspection four times/year. By contrast, the Occupational Safety and Health Administration (OSHA) does not have a similar frequency of inspection requirement. Even without the presence of MSHA, though, promoting and protecting employee safety and health is a core value in our industry.
Workplace Health
Respiratory health has a long history within the cement industry, and it is a topic of consistent focus. Cement manufacturing is multifaceted, and companies formulate, implement and periodically evaluate respiratory protection among employees to guard against dust exposures. Cement plants consider all other conditions affecting miners' health, such as exposure to excessive noise and hazardous materials. Hearing conservation programs require baseline audio testing and subsequent tests.
Workplace Safety
Cement manufacturers have formal safety programs for all stages of production, from quarrying to packaging and distribution.
Workplace examinations before starting work, during work, and after work are an integral part of the safety at cement plants and distribution terminals. Detailed checklists provide guidelines for managers and hourly employees alike, and plant operators formally note correction of items discovered during inspections that require repair and maintenance. Employers and employees participate in safety meetings on a regular schedule, including daily, weekly, monthly, and yearly. Cement manufacturers place their highest focus on making sure employees go home every day in the same shape they arrived at work.
MSHA-PCA Alliance
PCA has been a proud Alliance partner with the Mine Safety and Health Administration (MSHA) since 2008. The MSHA-PCA Alliance brings together industry with agency staff to improve worker health and safety through education, training, outreach, and communication. PCA staff and OHS members meet with the Assistant Secretary and senior MSHA staff twice annually to discuss health and safety issues and collaborate to improve worker health and safety. Key trainings have been developed over the last decade to enhance awareness about prominent safety issues, and regular safety newsletters are sent to PCA member company CEOs to keep them apprised of safety data trends and ways to continually improve their safety programs.
For a list of COVID-19 Resources click here.
For a list of COVID-19 State Resources and Environmental Policies click here.