Whether they think of it as “building green” or “sustainability,” today’s consumers expect their homes to have minimal environmental impact yet meet or exceed their lifestyle needs. They want properties offering comfort and security with low energy bills and low maintenance. They also demand healthy interiors that promote well being. Moreover, they want all of this in an attractive package.
Contemporary concrete building systems offer features that purchasers and builders value: strong and solid construction that provides comfortable shelter and protects occupants from extreme weather. Yet strength and durability alone are not enough. The systems have to be easy to design and build and be versatile to suit any architectural style. Concrete systems deliver all that and more.
Even though many concrete building systems have been around for a long time, consumers may not be aware of them. PCA began a targeted promotion of concrete systems for residential applications in the mid-1990s, intended to introduce a new audience of buyers and builders to the wide variety of structural concrete products suitable for building homes. Construction of above grade walls for concrete homes increased from about 3 percent at that time to nearly 9.3 percent in 2012.
Table: Residential Market Share of Above Grade Concrete Walls
Sources: NAHB Research Center, ICFA, and PCA Market Research Surveys
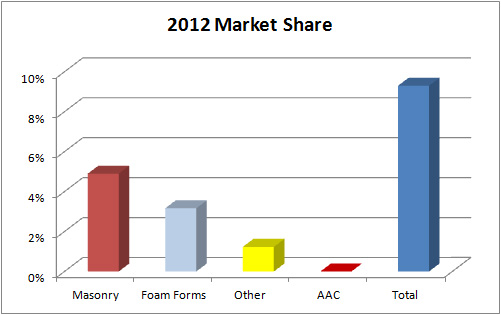
PCA now promotes concrete systems for residential and other low-rise structures. Most if not all of the benefits of concrete construction are suitable to both classes of buildings. The links below provide detailed descriptions of each wall system and important characteristics of them.
Autoclaved Aerated Concrete (AAC)
Autoclaved aerated concrete is made with fine aggregates, cement, and an expansion agent that causes the fresh mixture to rise like bread dough. In fact, this type of concrete contains 80 percent air. Made in a factory setting, the material is molded and cut into precisely dimensioned units. Read more on autoclaved aerated concrete (AAC).
Concrete Brick
Concrete brick is one of the oldest building materials. Primary raw materials for modern clay brick include surface clays, fire clays, shales or combinations of these. Along with striking visual qualities, brick also deaden exterior noise and can improve the thermal qualities of walls. Read more on concrete brick.
Concrete Masonry Units
Traditional concrete masonry units, referred to as “CMU” and sometimes “block,” have a long history of use for basements and above-grade walls of homes. Available in plain units finished with other materials or architectural units that remain exposed to view, they can be insulated, reinforced, and grouted to form energy efficient, strong building envelopes. Read more on concrete masonry systems (CMS).
Insulating Concrete Forms (ICF)
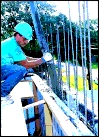
As lightweight modular panels or blocks, ICFs combine easy form placement with a finish concrete wall encased between two layers of insulation. These systems have established themselves as environmentally friendly solutions to comfortable, durable buildings for housing and many other applications for low-rise construction. Read more on insulating concrete forms (ICFs).
Panel Systems: Precast and Tilt-Up
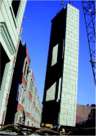
There are two main types of panel systems used for concrete walls: precast concrete and tilt-up concrete. Both types of panels are typically erected with a crane, but differ in where they are cast. Precast concrete panels are built in a controlled manufacturing facility and shipped to the site on trucks. Tilt-up panels are site cast from ready-mixed concrete, usually formed on top of the floor slab, for minimal site disruption. Flat casting simplifies the concreting process and panelization offers an opportunity for repetition and walls that go up fast. Read more on precast concrete. Read more on tilt-up concrete.
Removable Forms (Cast-in-Place)
Casting concrete in place involves the use of removable, forms, typically made of aluminum. Rigid foam insulation is often placed between forms and fastened with a system of non-conductive ties before concrete pouring begins. The result is a solid wall with thermal mass and good insulating abilities. Read more on removable forms (cast-in-place) concrete.
Shotcrete
Shotcrete is a process where concrete is projected or "shot" under pressure using a feeder or "gun"onto a surface to form structural shapes including walls, floors, and roofs. Read more on shotcrete.