Since the first strip of concrete pavement was completed in 1893, concrete has been used extensively for paving highways and airports as well as business and residential streets. There are four types of concrete pavement:
- Plain pavements with dowels that use dowels to provide load transfer and prevent faulting,
- Plain pavements without dowels, in which aggregate interlock transfers loads across joints and prevents faulting,
- Conventionally reinforced pavements that contain steel reinforcement and use dowels in contraction joints, and
- Continuously reinforced pavements that have no contraction joints and are reinforced with continuous longitudinal steel.
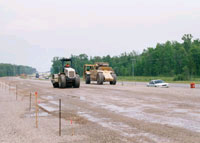
To prepare for paving, the subgrade—the native soil on which the pavement is built—must be graded and compacted. Preparation of the subgrade is often followed by the placing of a subbase—a layer of material that lies immediately below the concrete. The essential function of the subbase is to prevent the displacement of soil from underneath the pavement. Subbases may be constructed of granular materials, cement-treated materials, lean concrete, or open-graded, highly-permeable materials, stabilized or unstabilized. Once the subbase has hardened sufficiently to resist marring or distortion by construction traffic, dowels, tiebars, or reinforcing steel are placed and properly aligned in preparation for paving.
There are two methods for paving with concrete—slipform and fixed form. In slipform paving, a machine rides on treads over the area to be paved—similar to a train moving on a set of tracks. Fresh concrete is deposited in front of the paving machine which then spreads, shapes, consolidates, screeds, and float finishes the concrete in one continuous operation. This operation requires close coordination between the concrete placement and the forward speed of the paver.
In fixed-form paving, stationary metal forms are set and aligned on a solid foundation and staked rigidly. Final preparation and shaping of the subgrade or subbase is completed after the forms are set. Forms are cleaned and oiled first to ensure that they release from the concrete after the concrete hardens. Once concrete is deposited near its final position on the subgrade, spreading is completed by a mechanical spreader riding on top of the preset forms and the concrete. The spreading machine is followed by one or more machines that shape, consolidate, and float finish the concrete. After the concrete has reached a required strength, the forms are removed and curing of the edges begins immediately.
Joints Control Cracking
After placing and finishing concrete pavement, joints are created to control cracking and to provide relief for concrete expansion caused by temperature and moisture changes. Joints are normally created by sawing.
Once joints have been inserted, the surface must be textured. To obtain the desired amount of skid resistance, texturing should be done just after the water sheen has disappeared and just before the concrete becomes non-plastic. Texturing is done using burlap drag, artificial-turf drag, wire brooming, grooving the plastic concrete with a roller or comb equipped with steel tines, or a combination of these methods.
The chosen method of texturing depends on the environment, and the speed and density of expected traffic. Curing begins immediately after finishing operations and as soon as the surface will not be marred by the curing medium. Common curing methods include using white pigmented liquid membrane curing compounds. Occasionally, curing is accomplished by waterproof paper or plastic covers such as polyethylene sheets, or wet cotton mats or burlap.
As the concrete pavement hardens, it contracts and cracks. If the contraction joints have been correctly designed and constructed, the cracks will occur below the joints. As the concrete continues to contract, the joints will open-providing room for the concrete to expand in hot weather and in moist conditions. Once the pavement hardens, the joints are cleaned and sealed to exclude foreign material that would be damaging to the concrete when it expands. The pavement is opened to traffic after the specified curing period and when tests indicate that the concrete has reached the required strength. Immediately before the pavement is opened to public traffic, the shoulders are finished and the pavement is cleaned.
More information on concrete pavement may be found at the American Concrete Pavement Association web site.