Ultra-High Performance Concrete (UHPC) is a cementitious, concrete material that has a minimum specified compressive strength of 17,000 pounds per square inch (120 MPa) with specified durability, tensile ductility and toughness requirements; fibers are generally included in the mixture to achieve specified requirements.
Ultra-High Performance Concrete (UHPC), is also known as reactive powder concrete (RPC). The material is typically formulated by combining portland cement, supplementary cementitious materials, reactive powders, limestone and or quartz flour, fine sand, high-range water reducers, and water. The material can be formulated to provide compressive strengths in excess of 29,000 pounds per square inch (psi) (200 MPa). The use of fine materials for the matrix also provides a dense, smooth surface valued for its aesthetics and ability to closely transfer form details to the hardened surface. When combined with metal, synthetic or organic fibers it can achieve flexural strengths up to 7,000 psi (48 MPa) or greater.
Fiber types often used in UHPC include high carbon steel, PVA, Glass, Carbon or a combination of these types or others. The ductile behavior of this material is a first for concrete, with the capacity to deform and support flexural and tensile loads, even after initial cracking. The high compressive and tensile properties of UHPC also facilitate a high bond strength allowing shorter length of rebar embedment in applications such as closure pours between precast elements.
UHPC construction is simplified by eliminating the need for reinforcing steel in some applications and the materials high flow characteristics that make it self-compacting. The UHPC matrix is very dense and has a minimal disconnected pore structure resulting in low permeability (Chloride ion diffusion less than 0.02 x 10-12 m2/s. The material’s low permeability prevents the ingress of harmful materials such as chlorides which yields superior durability characteristics.
Some manufacturers have created just-add-water UHPC pre-mixed products that are making UHPC products more accessible. The American Society for Testing and Materials has established ASTM C1856/1856M Standard Practice for Fabricating and Testing Specimens of Ultra High Performance Concrete that relies on current ASTM test methods with modifications to make it suitable for UHPC. The following is an example of the range of material characteristics for UHPC:
Strength
Compressive: 17,000 to 22,000 psi, (120 to 150 MPa)
Flexural: 2200 to 3600 psi, (15 to 25 MPa)
Modulus of Elasticity: 6500 to 7300 ksi, (45 to 50 GPa)
Durability
Freeze/thaw (after 300 cycles): 100%
Salt-scaling (loss of residue): < 0.013 lb/ft3, (< 60 g/m2)
Abrasion (relative volume loss index): 1.7
Oxygen permeability: < 10-19 ft2, (<10-20 m2)
Figure 1. Shawnessy Light Rail Transit Station,
Calgary, Canada
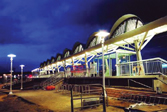
First Use of Ultra-High Performance Concrete for an Innovative Train Station Canopy
By V. H. Perry and D. Zakariasen, Lafarge Canada Inc.
The Shawnessy Light Rail Transit (LRT) Station, constructed during fall 2003 and winter 2004, forms part of a southern expansion to Calgary’s LRT system and is the world's first LRT system to be constructed with ultra-high performance concrete (UHPC). The innovative project, designed by Enzo Vicenzino of CPV Group Architects Ltd., is owned by the City of Calgary, managed by the Transportation Project Office (TPO), and constructed by general contractor, Walter Construction.
The Design
The station's 24 thin-shelled canopies, 16.7 feet by 19.7 feet, and just 0.79 inch thick, supported on single columns, protect commuters from the elements. Ultra-high performance concrete has a unique combination of superior technical characteristics including ductility, strength, and durability, while providing highly moldable products with a high quality surface aspect. The contract document specified a minimum requirement of 19,000 psi. In addition to the canopies, the components include struts, columns, beams, and gutters. The volume of material used totaled 105 cubic yards.
Manufacturing and Installation
The precast canopy components were individually cast and consist of half-shells, columns, tie beams, struts, and troughs. Table 1 summarizes test data from production of the twenty-four canopies.
Figure 2. Half-canopy in steel form
The columns and half-shells were injection cast in closed steel forms (Figure 2). Troughs were cast through displacement molding, while struts and tie beams were produced using conventional gravity two-stage castings.
The columns were installed on the concrete platform first. Then, the right and left half-shells, along with
the tie beams, were pre-assembled in the plant and transported to the site where they were lifted (by crane) over the railway tracks, for placement on the columns (Figure 3). Upon arrival at the site, the canopies were set on temporary scaffolding, and struts were attached to the shells and previously installed columns with welded connections.
Figure 3. Canopies ready for transportation
Conclusion
The material's unique combination of superior properties and design flexibility facilitated the architect's ability to create the attractive, off-white, curved canopies. Overall, this material offers solutions with advantages such as speed of construction, improved aesthetics, superior durability, and impermeability against corrosion, abrasion and impact—which translates to reduced maintenance and a longer life span for the structure.
Iowa Boasts First Ultra-High Performance Concrete Highway Bridge in United States
Iowa’s Wapello County boasts the first ultra-high performance concrete(UHPC) highway bridge in the United States, completed in May 2006. Although a simple, single-span bridge with a three-beam cross section, the Mars Hill Bridge is a significant step toward “The Bridge of the Future” – utilizing 110-feet UHPC girders that do not have any rebar for shear stirrups. The project was one of 96 presented at the 2006 Concrete Bridge Conference held in May in Reno, Nevada.
References
Lafarge North America Inc. Ductal Website
Perry, V.H."Q&A: What Is Reactive Powder Concrete?", HPC Bridge Views, No. 16, July/August 2001.